LIFE CASTING

I created a latex bald cap for my model however did not have a template so made up the size and then cut it to fit her. In future, I will take a bald cap template of my model to ensure that my bald cap fits properly. I feel this will save time when cleaning up the life cast and will also make the bald cap easier to apply. I ended up using masking tape to strap down the bald cap as it was too big around the nape.
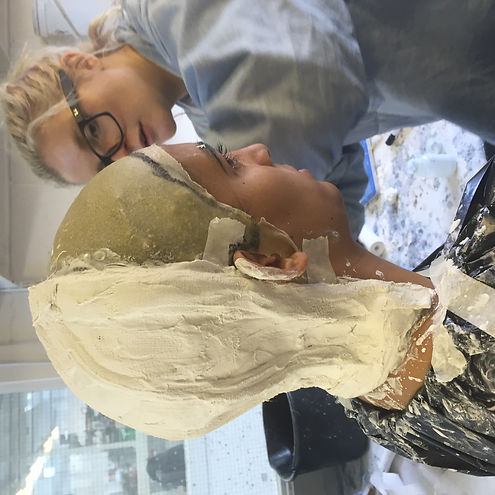
I left some space around the back of the ear and then did the plaster bandage for the back. This caused a bit of a problem with alginating, as it was difficult to get right behind the ear. Next time, I would rope right around the back of the ear.
I think I made my bald cap too thick, as it was hard to see the hairline to mark it out for reference. I did 10 layers of latex for this bald cap, next time I would perhaps use 6/7.

During the life cast, I noticed thatone of my helpers was not folding the plaster bandage. I always fold my bandage for extra strength, and this therefore made it difficult to know how many layers we had done. In future I will ensure that we are all on the same page in that sense.

I decided to use alginate rather than silicone, as it is far easier to clean up a plaster core than it is a fiberglass core. Alginate is also used far more in industry as it is much cheaper and therefore I would like to get more confident with using it.
I used plaster bandage at the back of the head as I did not need any detail from the back, therefore alginate was not necessary.

Cleaning Plaster Core

I am really happy with how my life cast came out - the face had no air bubbles in it. I think this is my best life cast yet. The ears cracked off when I was taking the alginate off however I expected this would happen as the ears are so delicate and hard to remove.

The plaster at the back of the head had lots of bubbles in it, where I used the plaster bandage with no alginate. The plaster also seemed to be adifferent texture on this side.

This shows the problems caused by an ill-fitting bald cap. Although it is not a problem, as once I have my models head measurements (I forgot to take these during the life cast - must remember to do this in future life casts) I will be able to shave the head down and fill in the air pockets with plaster. If this was a fiberglass core, it would be far harder to clean up and I would need to use car body filler - would not get a neat looking core.
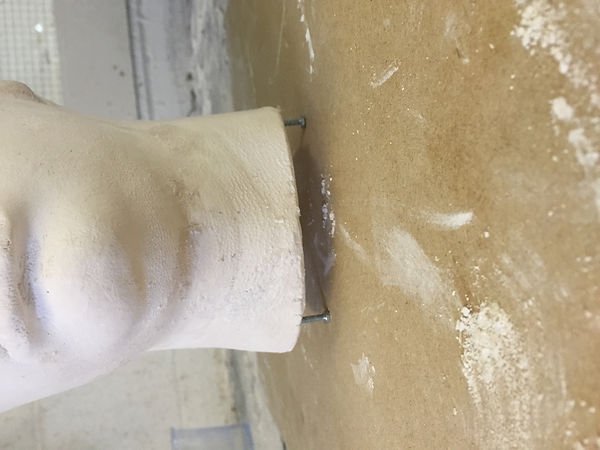
In Neill Gortons moulding DVD he suggests drilling into the life cast with 2mm screws. He then wraps around the screws with plaster bandage which I then did. I then filled around these screws and bandage using plaster. After that I smoothed the plaster down and neatened it up.
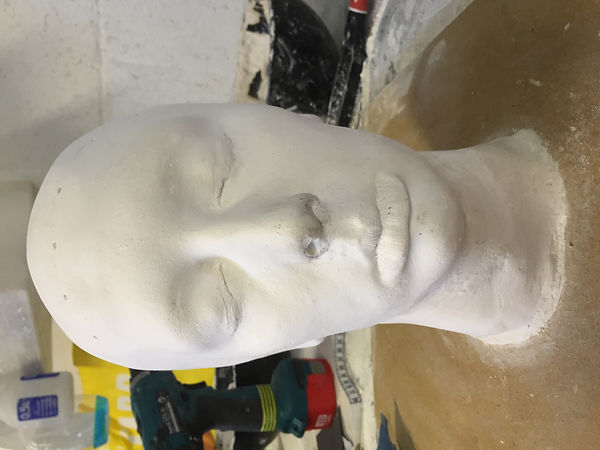
I spent a lot of time cleaning up my life cast as I feel this is an important stage. If the plaster core is not good quality then the end fiberglass will not be good. Another tip I learnt from the NG DVD was to drill 2mm holes all around the hair line - this may be particularly useful as I may need to sculpt a silicone bald cap. I then wrasped the ears down however left a little bit of the ear lobe as it is a good reference for where the ear is. I made sure it was rounded off to avoid an unecessary under cut. I tried using wet and dry sand paper to finish off my sanding however found it hard to use. I decicded to try a very fine sand paper which worked much better.
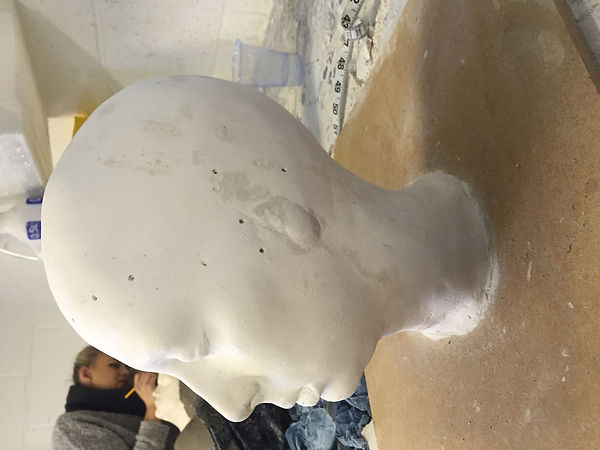
I found it tricky rebuilding the correct anatomy once I had sanded down the propblem areas at the back of the head. It is these difficulties I may be able to avoid if I use a well fitted bald cap in future.
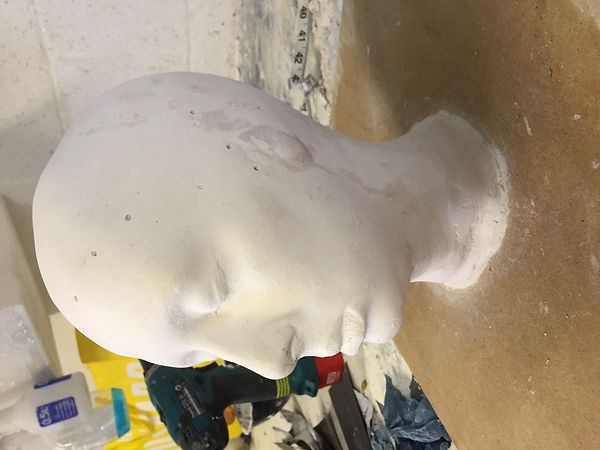
Silicone Layer
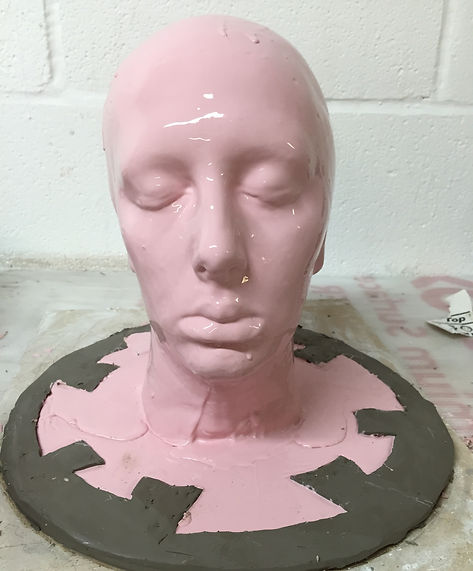
I'm a paragraph. Click here to add your own text and edit me. It's easy.

Next, I built a clay wall around the bottom of my head to stop the silicone from flooding. I made dovetail keys evenly and tred to make the wall as clean as possible.
I then weighed out my silicone and catalyst. The mixing process of this is quite vigorous and therefore creates air bubbles in the silicone. Through my research, I knew that it was import to 'degas' the silicone to get the air bubbles out. This is important, as the first thin layer is the detail layer and do not want airbubbles when i come to to fiberglass.
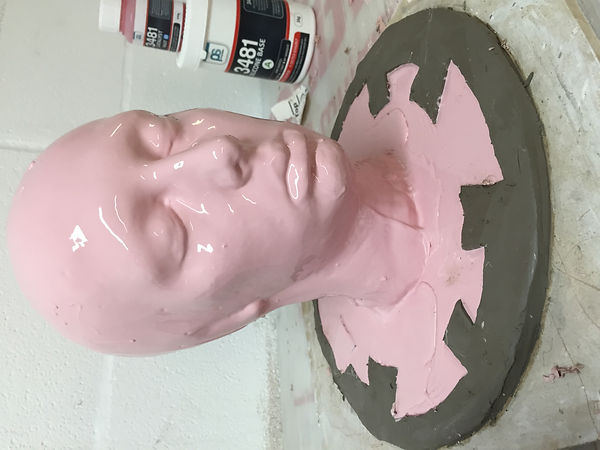

I made some silicone keys and placed them down the side, as my mould is going to be a two part jacket which will go along that line. I also put keys at the back and the front as it is important to have key points in places where there is vast amounts of 'nothing'. The face is less important as the features are all in one place and do not require a key.


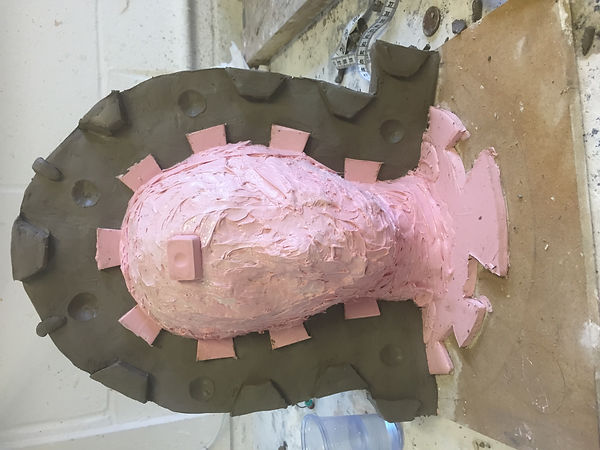
I used my Tiranti 92 to make the clay as smooth as possible and found this to be a really useful tool for this process. It really helped me to get a flush edge.
For this project I am really taking my time and concentrating on making my work neat and of a high quality compared to rushed like my last project. I found that due to rushing my work, I encountered more issues in the long run.
Fiberglass
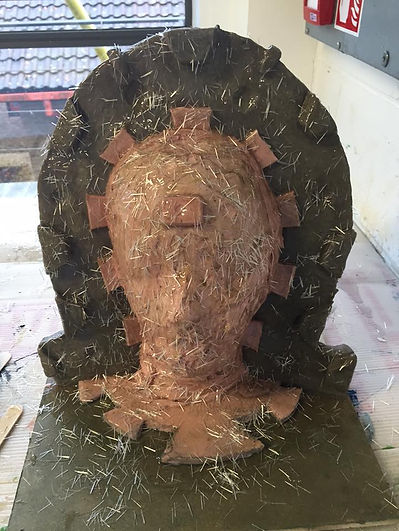
I used hairspray to seal the clay however it turns out this was not strong enough to seal it, and the water within the clay was preventing my gel coat from setting. Next time I will use lacquer on the clay to ensure it sets. I used PVA release on the board - I used this instead of wax because the wood is porous and PVA is better for releasing fiberous materials, whereas wax is better for fiberglass. I also used chopped strand as it helps the gel coat and the matting to bond together better.

On my first side of the jacket, I had problems with air bubbles around my keys. Ben suggested making a chopped glass paste and creating more of a curve, as it is the 90 degree angle of the key which makes it more difficult to lay up the matting.
I found this tricky at first however got used to it the more I did it.

I am feeling very frustrated with myself after my afternoon fiberglassing. Recently I have been really trying to take my time with my work as I am aware that rushing it causes more problems. Today I let the pressure get the better of me and I rushed my fiberglassing.
I have been having problems with air bubbles and I still had issues even with the chop paste. Mould making is an area I really want to focus on improving as I do find processes such as fiberglassng difficult to get right.
I think I need to be more methodical when fiberglassing, ensuring that I am using a 'routine' to make sure that I am laying an even coverage. I I must take my time otherwise I will not get a good mould. I am glad I have realised this now - before I start fibreglassing my core. I must also make sure I am using enough resin, but also not too much, as too mich resin will make my mould weaker.
This is an important area for my own critical evaluation, as it is an area I must do my best to improve and find where my problems are stemming from (e.g. rushing!!).
This was my first core which came out of the mould warped and under pigmented - Next time would need slightly thicker second layer of gel coat and put more pigment in the first layer. Use chop paste.
This wasmy second attempt at a core which was much more successful.
It turned out that I did not need to use the core as I did not need to create a silicone bald cap.
I needed to go through these processes as it was a contingency in case a flocked plastic cap was not effective.
It was good to practice my life casting skills and mould making. I

