MASTER SILICONE NEGATIVE MOLD

Attach plaster cast to base board - MDF - not too thin - too flexibily
Surface of wood sealed with Shellac, stops surface being porous



needed more space to sculpt down to. do not use screws that are too big as may crack the cast.
makes anchor points into the board - drill screws at an angle on the base
Build up plaster bandage around the nails and then use plaster to fill the space between the cast and the board between the nails.
Clean the excess plaster off the board using a spatula once dry.



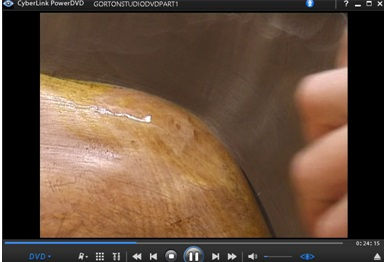


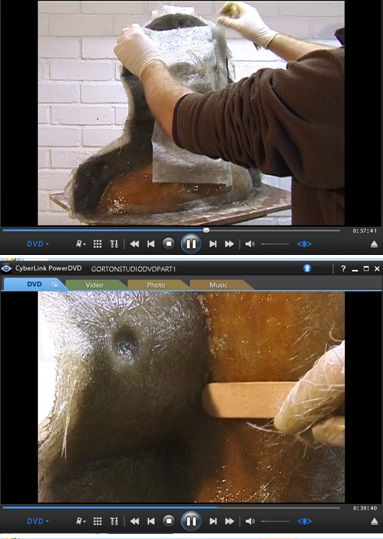

Brush Shellac onto the plaster core. The layers saturate the plaster and as they dry, it seals it. - if using fiberglass straight onto surface - because there is no detail.
No need to shellac the front because we will be using silicone and creating the clay wall - as the clay does not curve nicely - add slices into the clay. Trim wedges of clay to fill the gaps. Gorton goes around the ear, with ear on front side.
Rough wall. clay all around the base to strengthen. Paper towel pinned in place and spritzed with water.
Cover clay with plaster banadage - this is to add strength so that you can work on the wall without it falling
Strips across of plaster bandage - not too much bandage as it will be hard to remove.The neater and the smoother the wall - the better the join of the mould
use slightly damp sponge to clean the clay - need a sharp 90 degree angle
Little keys using a rubber on end of a pencil - sprayed with wax first.
Bigger keys closer to the edge - find a good tool/object which will make neat keys by digging out clay with it. Smaller keys close to the core.PVA brushed on after shellac - 2 coats - all over the life cast and the flange. Allow 1st layer to dry and then add another. also add to the wooden base. Next use a spray wax. 2 layers - allow to dry inbetween layers. brush with talc - make more matt to ensure the gel coat does not slide off.
Smooth the gel coat into all the corners - even surfacesmall keys - use cotton bud to make sure there is no airbubble.
Have strips of matting - lay down 4 or 5 at once, wet them with the resin and quickly put on surface of mould.
Dont wet down too many strips at once. the resin breaks down the glass - makes it malleable but too much resin will weaken and make it messy mould.
overlap the clay by 10 - 15 mm - otherwise the outside edge of moulds are often too weak.
if there is an airbubble beneath matt - and it cures, it will be a weak area.
First layer of matting is crucial. using end of a brush to poke the matting again into the small keys to get rid of any air bubbles.Flange first. Laminate it down. cover with another layer of matting. Only once the flange has two good layers, start work on the core.
Gorton then works with larger sheet, press down in the middle and then press down into the edges. as it softens it will stretch and conform to shape. Another big sheet to cover shoulders. Always overlap. 2 layers on back of head, third layer on the flange.
Perfect point where the knife will cut through the matting which ahs overlapped - saves using vibersaw.
Fiberglass has set, pull off the plaster bandage on front and gently start peeling back the clay. Remove what you can by hand and then use a metal tool to remove excess.




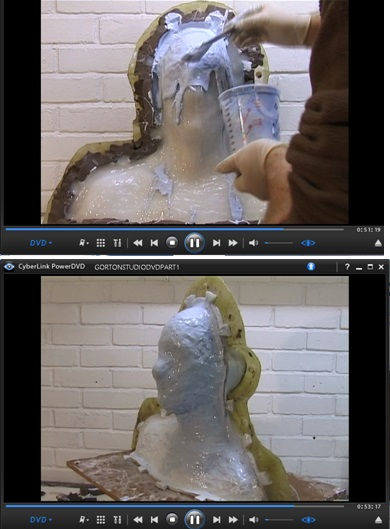

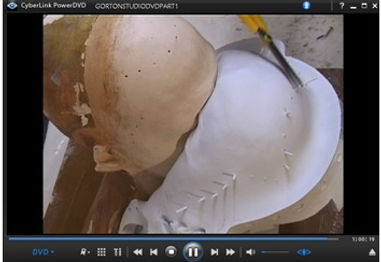
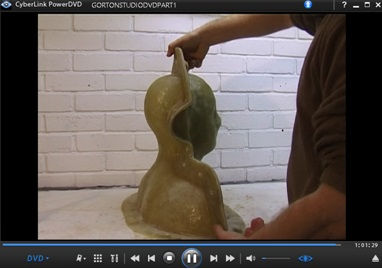
Gorton wants to keep the core & mould secure. will screw down into the base and one screw into the head to keep the fiberglass on.
Wall built to contain silicone.
Keys - dovetails 2 angled lines aiming outwards all the way around the head. Wall around the ear much higher, going to flood fill the ear with silicone.
2 silicones - Tinsil 7025 - standard mould making rubber, Tinsil spray 25 - thixotropic in this one, makes it easier to brush on.Start with the thin coat (7025). and then the tinsil spray 25.Apply a thin skin to capture all the detail - use half a kg at most. force out any airpockets.
Will be able to add more silicone after 2 or 3 hours. need to catch while still fresh - dust and material can settle and act as a separater.
Use thicker silicone - use spatula to smooth it on.
After a few hours once it is set, stand up and use a thin layer of silicone - brush coat over whole surface. will give smooth surface to work on. Leave over night to cure thoroughly.
Fiberglass the silicone to create jacket. spray two coats of wax as it is fiberglass on fiberglass - powder against. dont need wax on silicone as it is self releasing. only on flanges and wooden base. 2 layers around flange, then two on main piece, one more on flange.
Bolt mould together. remember to remove the scrws
RUBBER MALLET - gently tap until a line appears as it is only suction holding this together. then put tip of screw driver or chisel in - then pull apart.Pull silicone off.
trim the strips of silicone, but do not cut so that they are flush - leave a little (1mm) as it will help as you cast out positive - show where hairline is. Put silicone back into jacket mould.
PART 2



I'm a paragraph. Click here to add your own text and edit me. It's easy.
use wax to extend life of your silicone.
Dont want material on the flage - will prevent the two halves going together cleanly. BRush on layer of resin over the gel coat - do not over saturate. activate and bite into the resin - allow it to be matted. no gel coat or matting to go to flange - move matting around and keep 5mm from the edge lclean. use finger to push matting down tight to surface of gel coat in areas such as nose. make sure every square millmetre is tight to the gel coat. Do not over catalyze - will make it hard to stamp down matting. give yourself plenty of time. Has taken Gorton 1hr to matt. make sure you take your time.
Spring clips - no seam. put bolts and wing nuts to keep together, every second or third bolt.
apply resin to the seam
attach a paint brush to a piece of dowl to be able to apply resin in narrow neck. put matting on end of stick and position ccarefully, slide around until it is neatly over join and then laminate down. try not to disturb any of the other laminating on mould. 3 layers of matting on the seam as there is 3 layers on the back and front. equal thicknerss - or you will have weakness in seamPull apart. use rubber mallet again to tap surface. if it is well waxed, it will only be suction keeping together.
Car body filler if there is any 'steps' in the seam. add pigment if you want to so that it is seamless with rest of head cast.
Use car body filler on holes in forehead


keep shape of front of ear as it will act as a marker for prosthetics so that it fits face properly.
Character that he is sculpting has a large nose and will not need to get around nostril in subtle way. fill in these areas - can still see where edge of nostrils are - will make more practical for moulding later -less under cuts

Fig. 76